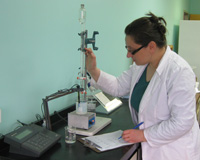
A Highbridge chemist performs chloride analysis on a concrete sample through a potentiometric titration with silver nitrate. When measured at regular intervals in a concrete element, a cross sectional profile of chloride permeation and concentration can be determined. It is important to establish this profile as both highly permeable and impermeable concrete may exhibit similarly elevated chloride levels along the surface where deicing salts have been applied.
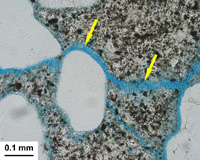
Not all cracks in parking structures are related to reinforcement corrosion. The arrows in the micrograph above indicate microcracks filled with ettringite. The cracks are found pervasively surrounding fine and coarse aggregate grains with a texture known as “ring fissuring”. While ettringite can be an innocuous deposit, its occurrence here is indicative of a much more serious condition called delayed ettringite formation (DEF) that causes expansive cracking when moisture is available. DEF is a problem unique to steam-cured precast elements or other concrete subject to higher temperature conditions during curing.
Parking Structures
Concrete used in parking structures is exposed to unique and often aggressive service conditions. Automobile exhaust and deicing salts tracked inside by vehicles are both agents that can accelerate the corrosion of steel reinforcement. Portions of the structure may be subject to water saturation and freeze-thaw cycles particularly along ramps and exterior walls. Original precasting methods may have resulted in expansive cracking due to delayed ettringite formation. Condition surveys and rehabilitation plans for parking structures can be complicated and must consider the distinctive environment and construction methods in order to guarantee success. Highbridge understands these unique conditions and tailors its examinations to provide economical solutions where a maximum of information is required on a square footage basis.
Highbridge will often recommend performing limited carbonation depth determinations and chloride ion contents at multiple depths for most probe locations as these are the primary culprits responsible for reinforcement corrosion. Petrographic examination and other testing may be performed on fewer probes particularly where secondary causes of cracking may be present or the general condition of the concrete must be determined.