Architectural Cast Stone and Concrete Masonry
While some think of cast stone as nothing more than precast concrete, the manufacturing methods, emphasis on aesthetics, and application result in performance issues that are unique to the material. The differences between dry tamp or wet cast methods of casting result in distinctive porosity structures that affect the porosity and permeability of the masonry. Aggregate choices based on appearance often results in the inclusion of alkali reactive materials responsible for deleterious cracking. Additional pathways for moisture along mortar joints means that salt distress or freeze-thaw expansion might occur “invisibly” in rough cast backing mixes behind higher quality facings. Petrography may be used to characterize the original mixtures and evaluate service performance. Where cast stone is present on historic structures, petrography is used in combination with chemical analysis to determine the original mix proportions and assist in developing a suitable replication mix.
ASTM C 1364 specifies performance criteria for cast stone including compressive strength (ASTM C 1194), hot and cold water absorption (ASTM C 1195), and freeze-thaw durability testing (ASTM C 666). Highbridge performs these tests for cast stone in addition to petrography and chemical analysis. Three dedicated freeze-thaw chambers are available at our facility accommodating up to fifty test specimens.
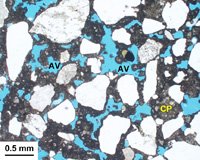 |
The two cast stone specimens are meant to simulate limestone but were cast with different materials and methods. The micrograph on the left shows a wet cast mix and the micrograph on the right a dry tamp mix. Both have relatively high porosity but different permeability structures. The non-air-entrained wet cast mix has few spherical air-voids (AV) while the dry tamp mix is poorly consolidated with an abundance of irregular compaction voids. In contrast, the cement paste in wet cast mix (CP) has a higher microporosity due to the original water content. This is seen by the absorption of blue-dyed epoxy used in the sample preparation. Note the much darker and denser cement paste in the dry tamp mix. The cold water absorption of the wet mix is lower but the masonry is susceptible to freeze-thaw damage due to the lack of air-entrainment. The dry tamp mix is more resistant to freezing damage but transmits water much more easily through the masonry.
|